- The analysis revealed that the recycled paper had less than one percent of the greenhouse gas emissions responsible for climate change and ocean acidification as the virgin paper, while using one-fourth of the water.
- The harvesting of the wood fed into just one of the virgin paper mills disturbed the habitat for 115 different endangered species.
- Virgin paper makers are attempting to rebrand their product as just as climate-friendly as recycled paper, while better suited to fine printing tasks.
A new life cycle analysis shows the substantial environmental benefits of 100 percent recycled paper over paper made from virgin wood fiber.
The study, conducted by SCS Global Services on behalf of New Leaf Paper, a company that specializes in “tree free” paper, is the first to use a new standard for evaluating the environmental impacts of a product’s complete life cycle. The results are perhaps not that surprising, but notable all the same.
SCS Global Services compared the environmental and human health impacts of 2,500 tons of New Leaf’s Reincarnation paper — 100 percent post-consumer coated paper — with the impacts from 2,500 tons of comparable virgin coated papers produced by three North American mills.
The analysis revealed that the recycled paper had less than one percent of the greenhouse gas emissions responsible for climate change and ocean acidification as the virgin paper, while using one-fourth of the water.
The use of recycled fibers, of course, also meant no logging occurred for New Leaf’s paper. The three virgin paper mills, on the other hand, required the harvesting of between nine and 18 million cubic feet of wood.
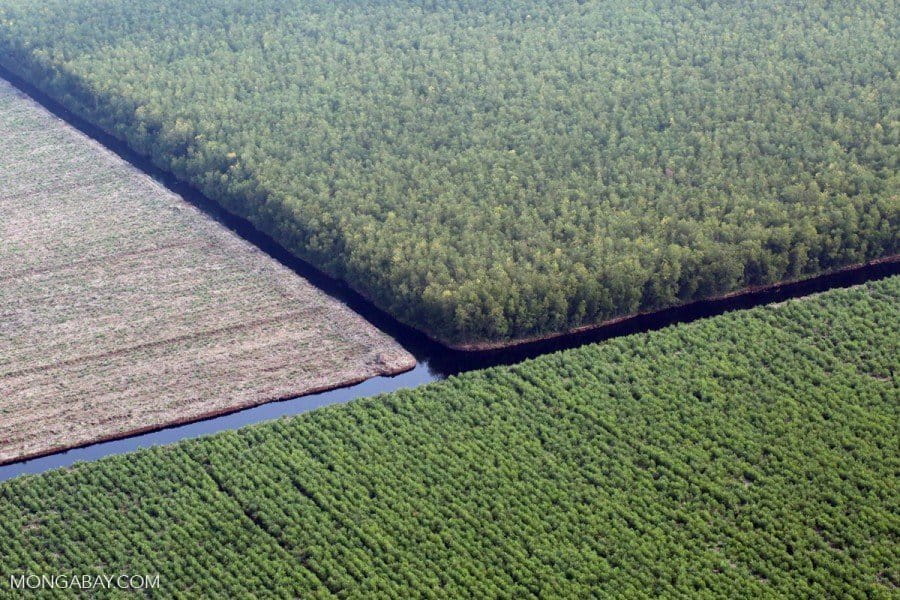
Recycled paper avoids the associated impacts that logging brings with it, too. For instance, the harvesting of the wood fed into just one of the virgin paper mills disturbed the habitat for 115 different endangered species. New Leaf’s recycled paper had no impact on rivers and wetlands, either, whereas the three virgin papers each impacted more than 600 watersheds.
Jeff Mendelsohn, who founded New Leaf Paper in 1998, said in a statement that he waited a long time for a rigorous, holistic life cycle analysis standard to emerge, and once it did he immediately requested a full analysis of his company’s recycled paper.
“New Leaf is proud to be driving transparency in the paper supply chain by commissioning this study featuring new methodology,” Mendelsohn said. “This study considers the full range of impacts and benefits, including incorporating the latest findings in climate science. It is a comprehensive and fair comparative analysis that sets a new baseline for future LCAs.”
Mendelsohn was probably also motivated to commission the study, at least in part, due to what he says is a push by large virgin paper makers like Sappi and Verso to rebrand their product as being just as climate-friendly as the recycled stuff, while more suited to fine printing and writing tasks.
In an op-ed he wrote for Triple Pundit in 2011, Mendelsohn argued that “making fine paper from waste paper is a more efficient process than making paper from trees, it uses less energy, less water, creating less effluent, and generating fewer greenhouse gas emissions.” Now he has even more evidence to back up that assertion.
New Leaf has partnered with Vancouver-based environmental non-profit Canopy to bring sustainably made paper to the US market for years (they helped ensure that North American editions of the Harry Potter books were printed on 100 percent recycled paper, for instance).
Nicole Rycroft, Canopy’s executive director, said in a statement that while all paper has some environmental footprint, this study “clearly shows that recycled papers are better for forests, species, freshwater systems and the climate.”
She also said the study’s findings should help drive home the importance of improving North America’s paper recycling system. “Given the superior ecological qualities of recycled paper, it is imperative that we bolster North American recycled paper production by curtailing recycled fiber exports and improving the quality of recovered fiber available to mills.”