- Aerostats—helium-filled payload-carrying balloons—can provide 24/7 aerial surveillance and communications with increasing reliability, safety, size and carrying capacity.
- Size matters: larger and higher quality aerostats can withstand rougher conditions, are safer and more durable, and carry larger, more advanced payloads, ranging from communications sensors to daytime and nighttime cameras, radars and other intelligence systems.
- Teams assessing the cost of operating an aerostat system, whether free-moving or tethered, must consider longer-term needs, including the required training for both aerostat and payload, number of technical teams, initial deployment process, routine logistical needs, helium supply and power supply.
Hot air balloons were the first airborne Intelligence, Surveillance, and Reconnaissance (ISR) systems, followed by hydrogen airships and blimps. With the advancement of aviation, these basic less-controllable platforms were consigned to recreational purposes.
In the last 30 years and even more so in recent years, as threats and technology have evolved and the need for 24/7 ISR has increased, helium-filled balloons—aerostats—have returned to the field. They are increasingly recognized as useful tools for long-term continuous ISR, as they overcome the greatest disadvantage of aircraft-based systems – limited fuel and flight time. They may also provide a visual deterrence to illegal activity, as they are lowered only for refueling and maintenance sessions.
![]() |
![]() |
As materials and technology have evolved, aerostats have increased in reliability, safety, size and carrying capacity. They can carry payloads—ranging from communications sensors to signals intelligence (SIGINT) and electronic intelligence (ELINT) systems, radars and day and night (cooled IR) cameras—with ever-higher reliability, range, quality and resolution. When evaluating the various systems for conservation work, potential users should keep their mission in mind (e.g. survey a reserve entry point, detect human intruders, relay communication, provide a 24/7 view of forest canopy, carry weather gauges or other research equipment) to effectively assess necessary coverage, mobility and permits from local air traffic control.
Navigating the range of aerostat systems – a summary
An aerostat is a craft that gains lift using a buoyant gas, such as helium or hydrogen, and therefore is lighter than air. All known field operational systems today use helium as their key “lifting” gas (it is non-flammable, so considered safer than hydrogen). Beyond that, aerostat systems vary greatly in quality, durability, simplicity, size and carrying capacity, creating a range of possible payloads, coverage, operation and cost.
Given this wide variety of platforms and components, we summarize here the main issues and factors that distinguish various aerostat systems—a Summary of a Beginner’s Guide to the world of aerostats. For a longer version of this guide, with details on each component, please see below the main post.
Operating an aerostat system requires two types of work:
- Controlling the aerostat by adjusting the helium content (lift), power supply and communication to the platform and anchoring, launching and maintaining the anchor base.
- Operating the payload, the actual work that monitors, communicates or gathers intelligence, depending on the mission.
Aerostats can be characterized generally according to several main parameters:
a. Component sub-systems: A majority of aerostat systems will include several sub-systems (Figure):
- the balloon itself (the aerostat)
- the “aerial unit” – the operational payload plus the hardware, communications and power systems needed to run it
- the operational payload – the sensors or devices performing the mission (survey, detect, communicate, etc.)
- the ground anchor unit that keeps the aerostat in place
- the operational station – where the ground controllers operate the system and payload
- the helium gas and support equipment to maintain the system over time
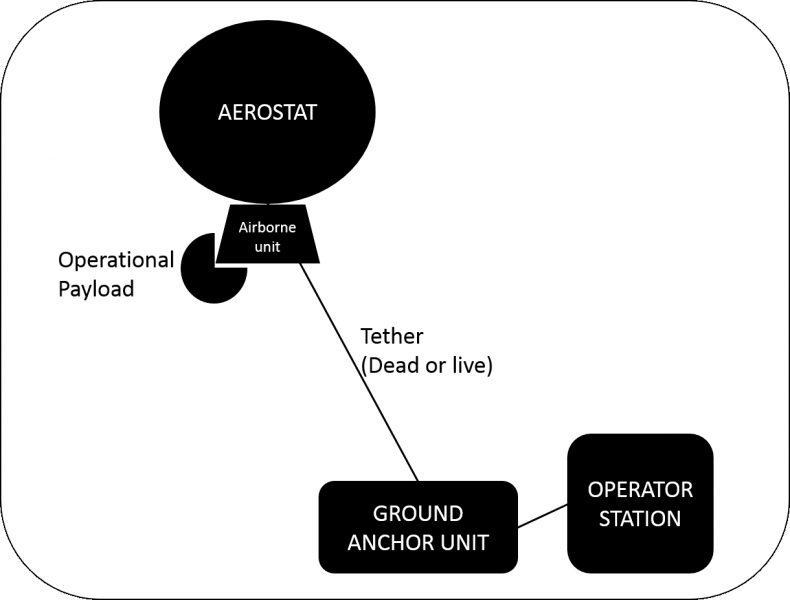
b. Shape: Aerostats can come in different aerodynamic shapes, from round to square, or shaped like a pumpkin, kite or fish. Each has advantages and disadvantages.
c. Size/Volume: The aerostat’s size, and thus its relative gas volume capacity, determines its capacity to lift the platform, cables, supporting gear and payload to its operational altitude. Size matters – larger systems generally carry heavier (read: better, longer-range) payloads and remain airborne in higher altitudes, over longer periods of time and in more challenging weather conditions than smaller ones. As you might expect, this greater capacity usually requires heavier, more complicated support structures, greater manpower and more power and helium.
d. Payload “carrying capacity”: The weight that the aerostat can lift beyond its own and its tether’s is its payload carrying capacity. It refers to both the “operational” payload, such as a camera, and the supporting systems that must be airborne with it (e.g. power, communication, computing, lights, etc.)
e. Operational altitude: The operational altitude is the “above ground” altitude at which the system is expected to operate while carrying the designated payload weight. Lift, and thus operational altitude, may change with external conditions, such as air pressure, and operators can lift the system to various altitudes within system limitations.
f. Tether/untethered: A tether is a specialized cable that anchors and connects the balloon to a ground anchor unit. Aerostats can be tethered to a stationary base or a mobile unit (e.g. a vehicle) or be completely untethered as flyable airships.
- In “dead” tether systems, the aerial unit must carry an independent power source (batteries) and wireless communication, so it is most common in smaller systems with low power needs.
- In “live” tether systems, the cable that secures the system to the ground base also transmits power and communication directly to the aerial unit.
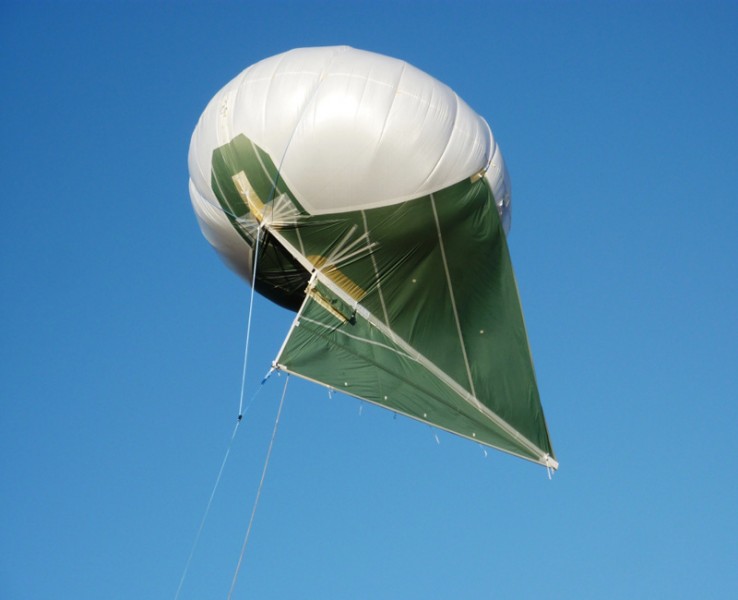
g. Power: Aerostat systems usually require a power supply—typically from the grid or a generator—for the ground unit, aerial unit and payload.
- Power to the ground unit ensures that the operator can lift, anchor, control and communicate with the airborne payload.
- In untethered and “dead” tethered systems, a single onboard power source (batteries) runs the aerial unit and payload. Battery weight decreases the operational payload’s carrying capacity.
- In “live” tethered systems, the power runs continuously through the tether cable to feed the aerial unit and payload; this allows the aerostat to remain airborne longer and carry a heavier operational payload, but both the system and maintenance cost more.
h. Communication: The main communication system transmits data from the aerial unit and payload to a ground station and commands from the operator back to the payload.
- In untethered systems, which function similarly to unmanned aerial vehicles (UAVs), and “dead” tethered systems, a wireless connection controls the platform and payload and transmits data down to the system operators. Wireless systems may demand more power and thus limit flight time and range, and the weight of wireless components on the aerial unit may lower the potential weight of the operational payload.
- In “live” tethered systems, the continuous cable-based communication between aerostat and ground extends the time the system is airborne and working and provides a more secure communication.
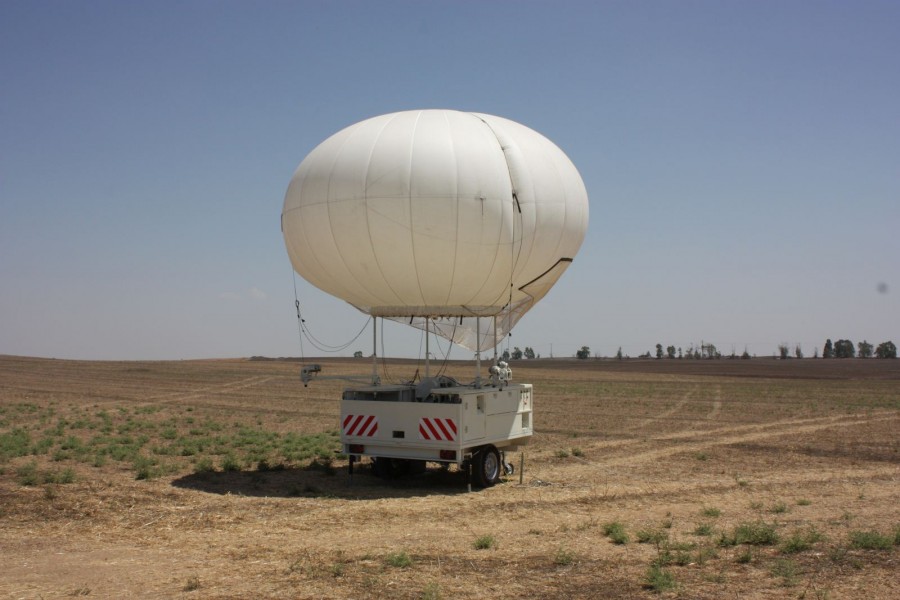
i. Operational Payloads: Aerostats can carry a variety of payloads, though most carry electro-optical (day and night cameras) or communication (e.g. relay) payloads.
- Larger aerostat systems with a continuous power source can carry larger, heavier payloads over longer periods of time.
- The operational “range” depends on the characteristics of the aerostat platform, flight altitude and payload. The same aerostat platform may be able to carry different payloads, depending on conditions and the design of the platform, station and payload.
j. Mobility: Aerostat systems can be flyable (UAV-like airships) or ground-tethered; ground-tethered systems vary in mobility.
- Flyable aerostat systems function like UAV systems and face similar limitations in flight time, distance range and weight capacity, as well as aerostat-specific challenges such as flight speed, helium loss and safety.
- Larger aerostats are generally stationary-tethered systems, as a heavy grounding unit is usually needed to anchor the aerostat and provide sufficient power, helium and communication to operate it. They must be disassembled before being transported.
- Smaller aerostats can be mobile-tethered systems, which include an anchoring unit heavy enough to secure the aerostat but light enough to be towed by field vehicles. These smaller systems, which fly lower and carry lighter payloads, can be anchored to an operator station or a strong stationary vehicle, which can tow a deflated or anchored aerostat.
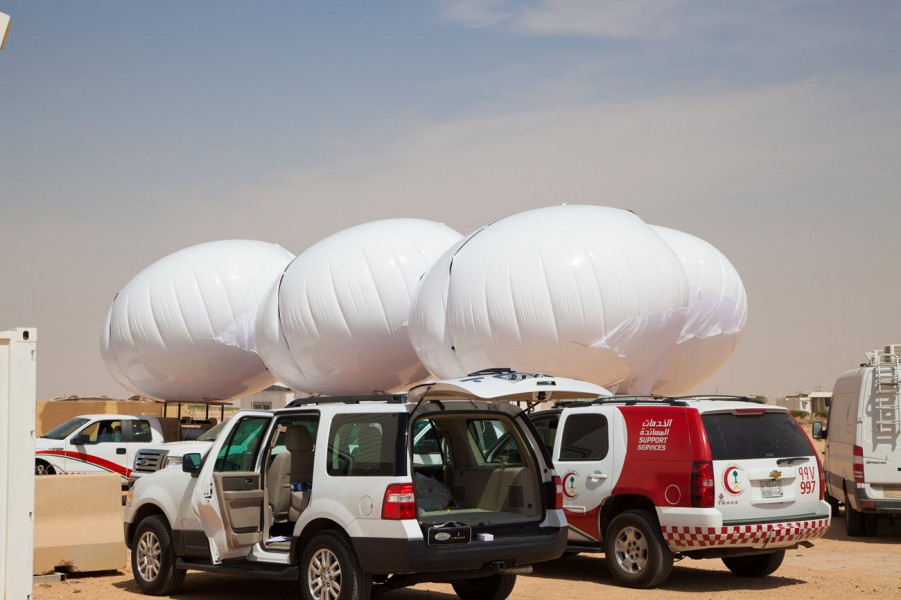
k. Limitations, Quality and Safety:
- Wind, air pressure and rain all affect aerostat operation; a higher-quality aerostat system can remain airborne longer and in harsher weather conditions while continuing to transmit quality payload data, but it will be more expensive and may require specific training and safety protocols.
- Any system with the aerostat or payload running day and night also requires shifts of operators to detect and respond to disturbance.
- Helium refueling requires the system to be anchored (not airborne). A consistent supply of helium is critical to the aerostat’s operation, so the gas must be part of long-term maintenance cost estimates.
Choosing a system
When considering using aerostats for conservation applications, teams should investigate a range of systems (various designs, sizes, mobile and stationary) with respect to their mission, particularly in the expected area of operation. Aerostats range from small systems flown at altitudes less than 100m (300ft), carrying payloads under 1kg for a short range, to heavy, long-range systems elevated to thousands of meters, carrying large payloads over 20kg with longer range of view or communications.
Aerostat pros: They provide constant vigilance and often deterrence, and they offer endurance, high reliability, simple operation and straightforward maintenance; they can be used daily, and some models are mobile. Tethered aerostats, more common than untethered versions, enable an aerial 24/7 point of view while also creating a visual deterrence to illegal activity.
Aerostat cons and costs: Aerostats are less permanent than towers, and they are not cheap. Initial cost varies widely within and among manufacturers and models, ranging from US$50,000 to $5 million for a full system. A medium-grade system’s cost (~US$200,000) is high for most conservation agencies. Larger, better-quality systems may require substantial user training, logistical coordination or Air Traffic Control permits, and they may be ITAR-limited.
The price depends on the system’s size, quality and reliability, which you’ll want to select based on the target mission for the aerostat (How far must its communication sensor range? How far must it detect a figure with its infrared camera? How rugged must it be, given weather and terrain?). Your mission therefore has to guide the selection, balancing need, quality and cost. Any assessment of the operational cost of a given system must take a long-term perspective and include in its calculations the required training, number of teams, initial deployment, life expectancy, routine logistical needs, required helium supply, power supply and other logistical costs (e.g. vehicles and fuel needed).
- Examples of systems: Raven, Skystar (100,180,200,250,300), Tcom (12, 17, 22), Lynx, Aeros3200.
- Examples of manufacturers: TCOM, Ravenaerostar, RosAeroSystems, RT, Aeros, Texas A&M (By RT).
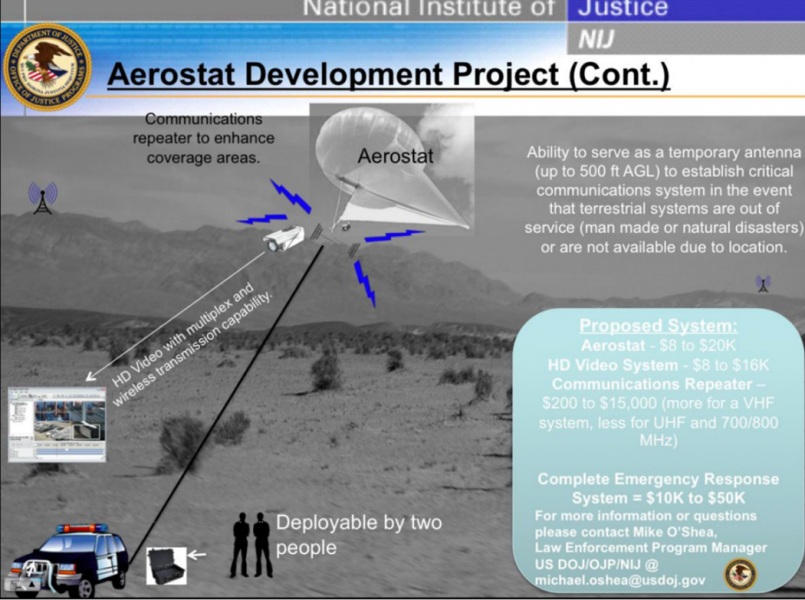
FOR THOSE SERIOUSLY INTERESTED in learning more about aerostats for reserve communication and protection, here are additional details on the parameters typically used to characterize aerostats:
a. Component sub-systems: A majority of aerostat systems will include some form of each of the following sub-systems.
- Aerostat – The aerial platform, creating lift and carrying the aerial unit. Aerostat is the common name for anchored/tethered systems, in contrast to non-tethered airships.
- Aerial unit – The aerial unit includes the “operational payload” and any supporting systems for its operation (communication, power, computers, lights, etc.)
- Operational payload – The unit performing the mission of the aerostat (electro-optical, SIGINT, ELINT, communication).
- Ground anchor unit – Aerostats require an anchoring unit that can resist the lift forces and secure the aerostat to its location. The ground anchor unit weight, size and complexity rise with aerostat size.
- Operational station – Aerostat systems lift operational payloads which are controlled from the ground-based operational station, including the downlink/uplink and user interface to fulfill the mission.
- Support equipment – The support equipment enables the long-term maintenance and operation of the system, including spare parts, anchoring tools, safety and emergency gear.
- Helium supply – The helium supply stability and quality is critical for the continuous operation of the aerostat system. Each model requires different supply routines.
b. Shape: Aerostats can come in different aerodynamic shapes, each with advantages and disadvantages, and the shape is determined by the systems concept of operation – tethered or non-tethered (piloted-flyable). Six common shapes are:
- Completely round, usually found in small tethered only systems or simple weather systems.
- Cone-shaped (stretched), usually found in meteorological and atmosphere research systems.
- “Pumpkin like” – found in medium to large tethered only systems.
- “Heli-kites” – relatively newer in the field, they have a pumpkin-like shape and an additional kite-like structure.
- Airship/fish-like – found in small to very large tethered and untethered systems.
- Square/Other – commonly found in larger, long-endurance, high-altitude systems.
c. Size/Volume: The aerostat’s size, quoted usually as its radius in round systems or its length and width in “fish” shaped systems, is a simple way to estimate its gas volume capacity and thus its capacity to lift the platform, cables, supporting gear and payload to its operational altitude.
- Volume matters – Gas volume determines lift capacity, and required volume may change with altitude above sea-level (air pressure) and time, as the helium gas leaks, breaks down and thus loses lift over time.
- Size matters – Generally speaking, larger systems can carry heavier (read: better, longer-range) payloads. Depending on payload, larger systems can generally remain airborne in higher altitudes, over longer periods of time, and in more challenging weather conditions than smaller ones.
- This greater capacity comes with a cost (no free lunch): larger systems tend to cost more to maintain, as they require heavier, more complicated support structures, greater manpower, more power, and more helium.
d. Payload “carrying capacity”: The weight that the platform (the aerostat) can lift beyond that of itself and its tether is its payload carrying capacity.
- Payload carrying capacity refers to the lift required to reach and operate at the expected operational altitude.
- Payload carrying capacity refers to the entire “aerial unit” and not only to the “operational” payload, such as a camera or other sensor, but to all its supporting systems that have to be airborne with it (e.g. power, communication, computing, lights, etc.)
- Coverage range takes into account the expected operational altitude and payload capabilities in a relatively flat terrain.
e. Operational altitude: The operational altitude is the “above ground” altitude at which the system is expected to operate while carrying the designated payload weight.
- The operational “above ground” altitude is usually calculated to sea level conditions.
- Operators can lift the system to whatever designated altitude they see fit as long as it is within system limitations.
- Lift, and thus operational altitude, may change with external conditions, such as air pressure, especially in areas substantially above or below sea level.
f. Tether/untethered: A tether is a specialized cable that anchors and connects the balloon to a ground anchor unit. Depending on size and design, systems can be tethered to a stationary base, to a mobile unit (on a vehicle) or completely untethered as flyable airships. Tethers can be roughly divided into two main types:
- “Dead” tether – Serves only for securing the aerostat to the ground unit, enabling launch and retrieval. These cables do not transmit any power or communication and are found more commonly in smaller systems with low power needs.
- In dead tether systems, the aerial unit must carry an independent power source in the form of batteries, and a wireless communication system.
- Depending on power needs (payload, communication, computer, lights), the systems will require periodic anchoring for power source replacement.
- “Live” tether – Has one main cable that can directly transmit power and communication to the aerial unit while also securing the system to the ground base.
- No additional power source is needed for live tether systems.
- The uninterrupted transmission enables prolonged operational time, as power can be fed continuously.
g. Power: Aerostat systems usually require a power supply for the ground unit (for lifting, anchoring, and controlling the aerostat), the aerial unit, and the payload.
- Power is usually supplied from the grid or from external power sources such as generators.
- Ground unit power – Provides power for both the ground anchor unit and the operational station.
- The anchor unit power serves to both lift and anchor the aerostat. Higher-level systems typically include a secondary backup power source (generator/batteries) for safety. Some smaller systems may not require power at all for lift/anchoring.
- The operational station power enables the operation of and communication with the airborne payload.
- In tethered systems, the operational station power is considered secondary and has almost no safety issues.
- In untethered (unmanned aerial) systems, operational station power is critical, as it is used to fly, operate and land the platform (like a UAV).
- Aerial unit/Payload power –
- In untethered systems (like a UAV), the same onboard power source is used for running the platform and payload.
- In “dead” tethered systems, the power to the aerial unit and payload comes from onboard batteries.
- This option – most common in smaller systems – is considered simple and safe.
- The weight of the batteries decreases the operational payload carrying capacity.
- Battery life limits the amount of time the system can remain airborne and requires regular changes in relatively small intervals (~hours), depending on your system and usage.
- In “live” tethered systems, the power runs continuously through the tether cable to feed the aerial unit and payload.
- Continuous power provides greater weight capacity for the operational payload.
- Continuous power enables longer airborne endurance and continuous work.
- Providing continuous power may cost more and maintenance can be more complex.
h. Communication: The main communication system transmits data from aerial unit and payload to a ground station and operator and commands from operator back to the payload. Some systems have secondary communication systems to transmit/receive data to and from external sources.
- Wireless (Cellular/Wi-Fi/Other) – In untethered systems (like UAVs) and “dead” tethered systems, a wireless connection enables control of platform and payload (uplink) while transmitting data down to the system operators.
- Wireless systems can transmit image and data to external units.
- Wireless systems may demand more power and thus limit flight time and range.
- With components located on the aerial unit, the weight of the communications system may lower the maximum possible weight of the operational payload (and a lower-weight payload usually means lower quality or capabilities).
- Cable-based (“live” tethered system) – Communication between aerostat and ground goes through the tether cable (on a separate cable or on the same power cable).
- May enable a greater weight capacity for the operational payload.
- Enables longer airborne endurance and continuous work.
- Provides a secure communication.
i. Operational Payloads:
- Aerostats are open platforms that, depending on the model and design, can carry a great variety of mission payloads.
- Most deployed aerostats carry electro-optical (day and night cameras) or communication (e.g. relay) payloads.
- Aerostat platform characteristics such as size, power and communication determine the expected payload carrying capacity and flight altitude. Larger aerostat systems with a continuous power source can carry larger, heavier payloads over longer periods of time.
- The operational “range” depends on the characteristics of both the aerostat platform (flight altitude) and the payload itself.
- The range depicted in many promotional materials relies on a specific manufacturer’s combination of components, under standardized conditions.
- The same aerostat platform may be able to carry different payloads, depending on needs, design of the platform, station, and payload, and conditions.
j. Mobility: Aerostat systems can be flyable (UAV-like airships) or ground-tethered; ground-tethered systems vary in mobility.
- Flyable aerostat systems function similarly to UAV systems and face some of the same limitations, including actual flight time, range, and weight capacity, while introducing new challenges such as flight speed, coverage, helium loss and platform specific safety.
- Stationary-Tethered systems are typically used for larger aerostats where there is a need for a heavy grounding unit that will be able to anchor the aerostat. The grounding unit includes the sub-systems that enable constant operation (e.g. power, helium, communication)
- A larger system will normally be able to operate at a higher altitude and carry heavier, longer-range payloads.
- The system must be disassembled before it can be transported.
- Mobile-Tethered systems use an anchoring unit that is heavy enough to anchor the aerostat but light enough to be towed by field vehicles.
- Small systems (lower altitude flight, lighter payloads) can be simply anchored to an operator station or a stationary vehicle.
- Medium systems (intermediate-altitude flight, small-medium payloads) require heavier anchors and are thus usually based on special towable anchors/vehicles.
- Mobile systems enable a compromise between flexibility and coverage needs, depending on the mission, team, field conditions, and operational plan.
- Mobile systems are normally not designed to be towed while airborne (Some are towable deflated or inflated but anchored).
k. Limitations, Quality and Safety:
- Aerostat systems are designed to be used in the field over long periods of time. Quality of design and manufacturing are critical to ensure satisfactory field performance over time.
- Systems of any size that are designed to meet military standards are usually highly reliable and superior quality but carry a much greater cost.
- Wind, air pressure, and rain are the main external factors affecting and limiting aerostat system operation.
- Generally speaking, quality is indicated by the system’s ability to remain airborne over longer periods of time, in harsher weather conditions while transmitting quality payload data in the required view range.
- Larger, higher-quality systems require additional training and safety protocols to ensure the safe and efficient operation of both the aerostat (platform) and the mission (payload).
- Any system running day and night requires operators (for aerostat and payload) in shifts that will be vigilant enough to detect and respond to any disturbance.
- The helium used for a given aerostat must match the required quality and be available in sufficient and regular supply for continuous routine operation.
- Helium supply must be included in calculating the long-term cost of maintaining an aerostat system.
- Helium fueling/refueling requires an anchoring of the system (it cannot be done while airborne).
Aerostats are most commonly used in their tethered version, though some recent military developments are aiming to produce quality untethered systems that can fly longer and higher than current models.
The use of a tethered aerostats enables an aerial 24/7 point of view, covering required areas day and night, creating in parallel a visual deterrence which is lowered only for short helium-refueling and maintenance sessions.
When evaluating their adaptation to conservation applications/needs, teams should investigate a range of systems (various designs, sizes, mobile, and stationary) with respect to the mission, particularly in the expected area of operation. Weather, terrain, and mandatory permits from local air traffic control will all affect the selection of an appropriate aerostat system.
Teams assessing aerostats must balance quality and cost. The target mission for the system should designate the quality needed, and any assessment of operational cost of a given system must take a long-term perspective and include in calculations the required training, number of teams, initial deployment, life expectancy, routine logistical needs, required helium supply, power supply, among other needs.
Due to a database migration error, the byline of this post was incorrect for a period of time. It was corrected on June 21, 2021